Food industry
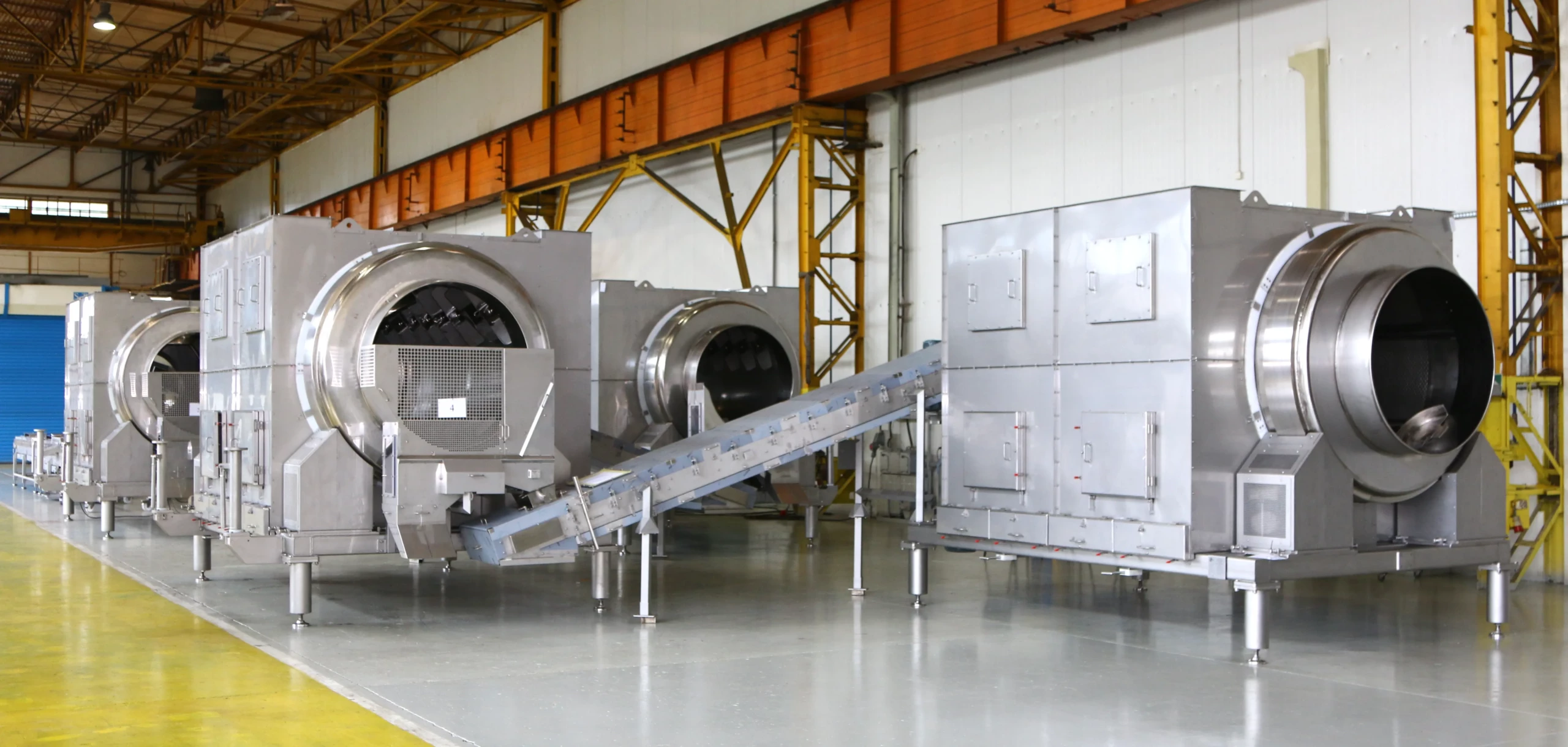
For the food industry, we manufacture mixers suitable for processing various types of confectionery, including chocolate-coated, hard-coated and soft-coated dragees. Our equipment can be used for applications such as dry and wet coating, polishing, smoothing and blending of confectionery products made from pastilles, dragees, expanded centres and various types of nuts. The capacities of our mixers are tailored to the customer’s process requirements and, in addition, we are able to supply them in a configuration suitable for continuous or batch operation, as required. In order to meet the most stringent hygiene requirements, all parts of the mixers in direct contact with the product are made from the highest quality AISI 316L stainless steel, ensuring safety and durability. Supporting structures and housings are made of durable AISI 304 stainless steel.
We can supply the equipment in the form of skids, which, in addition to the mixer itself, include: components for applying coatings in both liquid and dry form, loading and unloading lines and product transport systems. Our offer is complemented by the provision of maintenance services for the equipment supplied, from installation and supervision of commissioning to the provision of periodic technical inspections.
Polishing
Our polishing drums are designed to provide excellent results in smoothing and glossing the surface of confectionery and chocolate dragges. In the process of mechanical mixing with the presence of suitably selected coating agents, they allow a product with a high-quality finish to be obtained. To guarantee the protection of the batch being processed and to achieve an optimum end result, both the mixing drum and the discharge tunnels are rubber coated on the inside. The drum is positioned horizontally to the floor so that the load is evenly distributed over the entire length of it. This all guarantees a reproducible product finish.
The working cycle of the mixer is very simple and efficient. Once the mixing and polishing process is completed, automatic discharge is carried out by the reverse rotation of the drum. Discharge of the material takes place through discharge tunnels, through which it is directed to the receiver below. That can be a conveyor or intermediate hopper. To intensify the mixing process even further, our mixers can be equipped with specially designed mixing paddles.
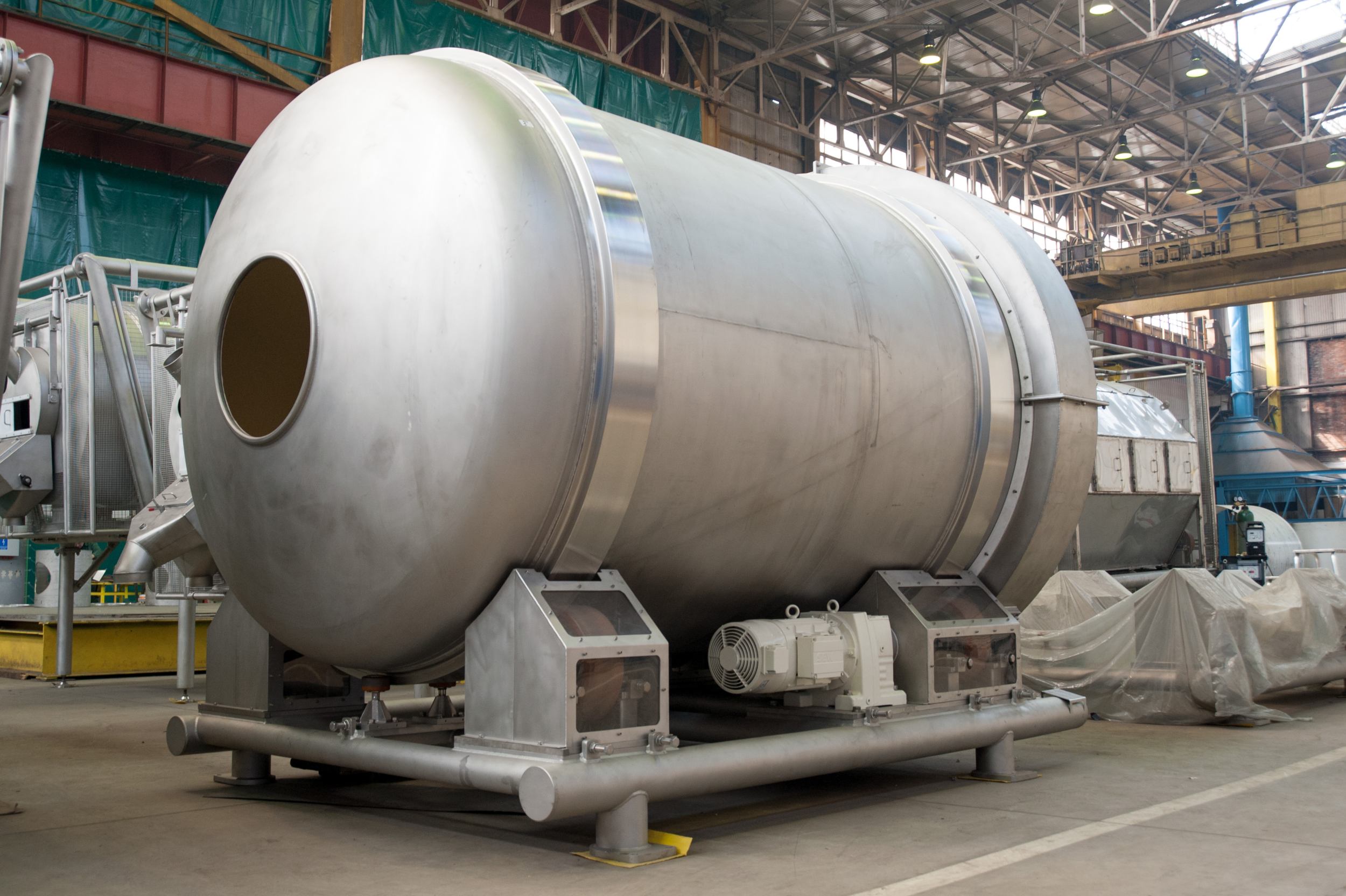
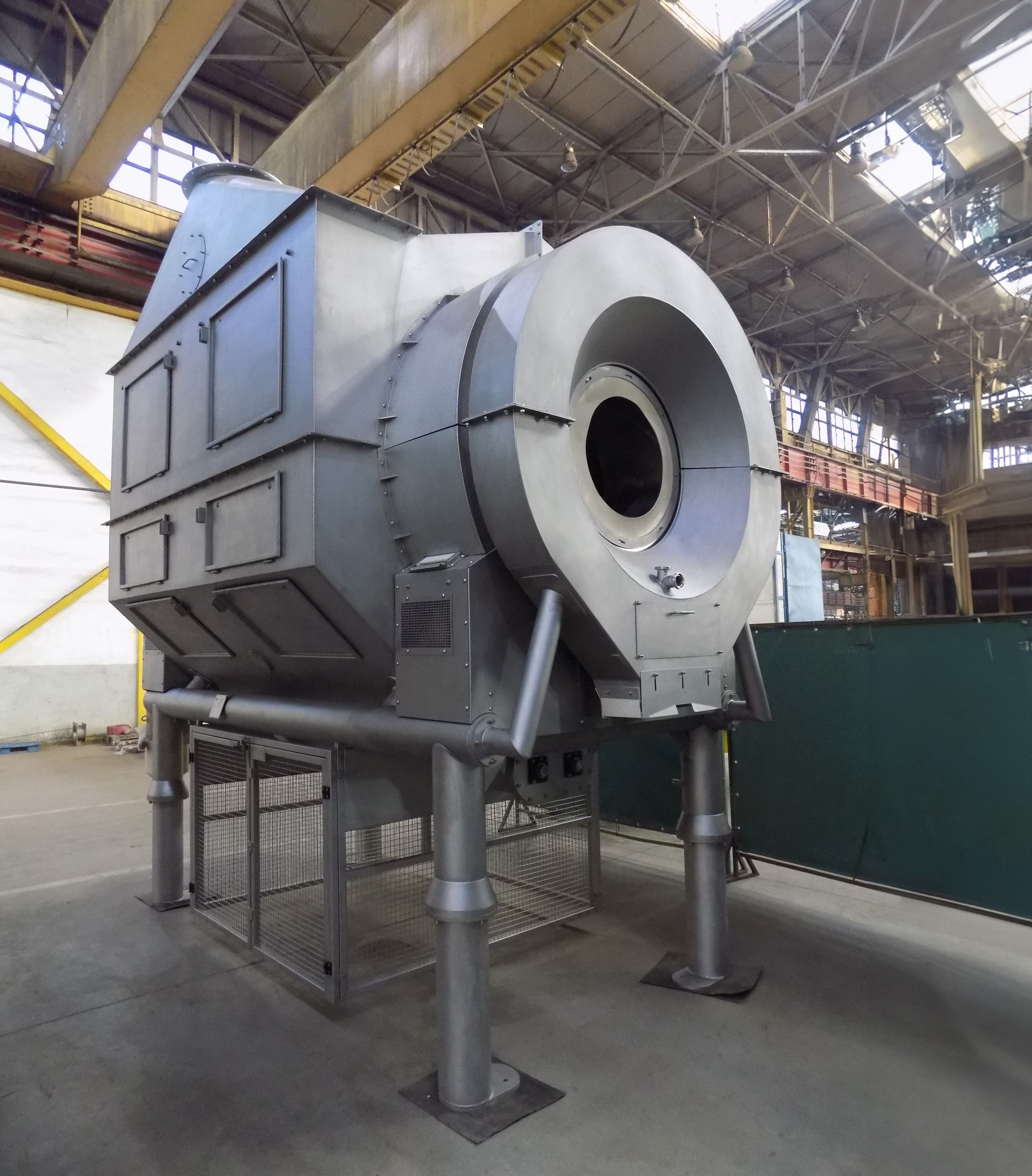
Dry/Wet coating
We are a supplier of mixers for both wet and dry product coating. Depending on the customer’s process requirements, we are able to supply units equipped with solid-wall or perforated-wall drums. The latter option, in combination with ventilation systems, allows adequate cooling of the processed product if required. The coating mixers can be adapted for batch or continuous operation. For the first option, the discharge of the finished portion of the batch stored in the drum is achieved by reversing the drum rotation, so that the product is directed through discharge chutes to external receivers. In the case of mixers operating in a continuous system, the flow of the product through the drum, while maintaining an appropriate filling level, is ensured by appropriate selection of the size of the drum inlet and outlet openings, the inclination of the drum axis in relation to the ground and the use of additional elements supporting the movement of the product such as spiral bands, paddles or mixing tunnels. The drive of the coaters can be implemented either through a system of rubberised drive rollers and race rings constituting the drum structure, or through a system of gear wheels. In the latter case, the drum is connected to the mixer support structure via slewing-bearings.
We have experience in designing and supplying coating mixers for sugar-type coatings with an integrated automatic cleaning system. This type of system on the one hand helps to reduce the process downtime and the number of maintenance staff required, and on the other hand, it allows the coating finish to be altered quickly for the next batch of product (e.g. by changing its colour).
We also supply continuous coating machines consisting of a set of drums on a single frame. They carry out the wet coating process followed by dry coating. The design is developed in such a way that the product passes directly from the “wet” drum into the “dry” drum. This type of design saves space and eliminates the need for additional transport systems between the drums. The support structure on which the drums are placed allows them to be automatically pulled apart, improving access to their interior for maintenance and service.
Tanks and Hoppers
To process the transport/storage of bulk materials, we offer our clients customised feeding/unloading systems. Our wide range of products includes conveyors, hoppers and tanks that can be tailored to suit a variety of applications. We offer both pressurised, low-pressure and non-pressurised tanks for a variety of purposes and capacities. Thanks to their high quality and fine engineering, these tanks are not only durable but also easy to clean, which is important for maintaining hygiene in production areas. We provide complete solutions that can be optimised to meet specific customer needs. Our systems are designed with support frames and access platforms and as ready-made skids, i.e. prefabricated modular units, for easy installation and integration into existing production infrastructure. The skids are tested before delivery, which reduces commissioning time and minimises disruption to the production process. On request, components in direct contact with the feed material can be made of 316Ti and 904L stainless steel. This ensures that our solutions are not only functional, but also meet the highest quality and safety standards.
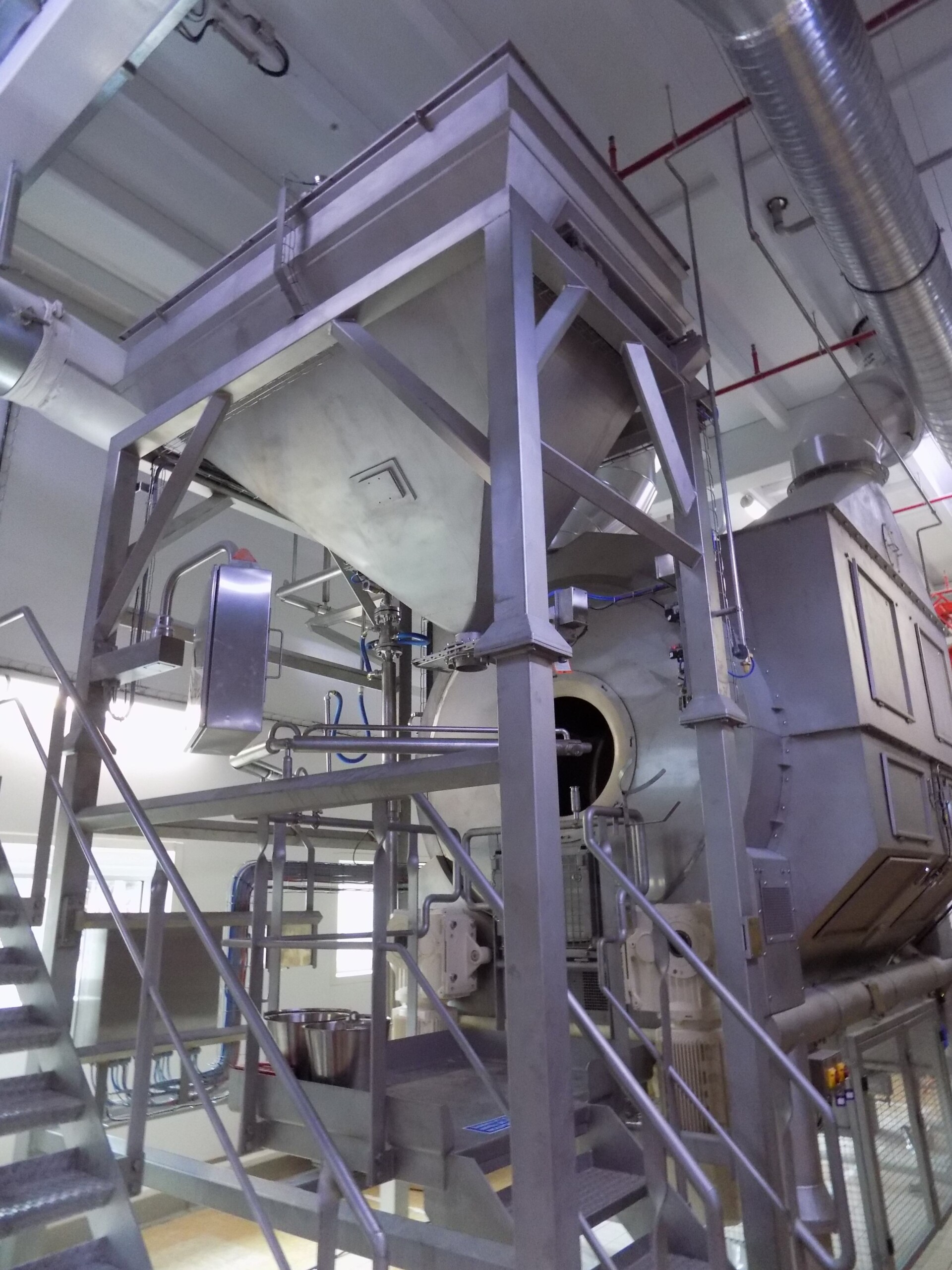